 |
Our Engineering and
Manufacturing departments are at the core of Alexis Fire
Equipment. The process of building a customized truck
starts with customer expectations and ends with customer
satisfaction. All aspects of manufacturing processes are
ultimately driven by and for the customer. How a task
is accomplished is the part controlled by Alexis Fire
Equipment. We thrive on innovation and producing apparatus
that not only exceeds expectations, but pushes the envelope
of conventional fire trucks. What you might have thought
was impossible in a truck can be brought to life with
our team of extraordinary engineers and skilled craftsmen. |
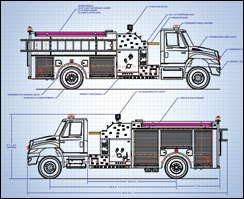
Cad Design
Two-dimensional blueprint of preliminary
truck body assures exact dimensions and maps general design.
|
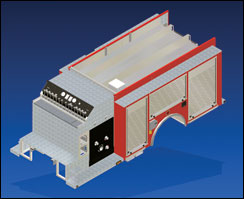
Solid Modeling
Three-dimensional drawings simulate
a virtual model shop and offer a greater definition of
compartment utilization. |
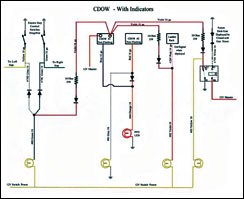
As-Built Wiring Diagrams
Customer-specific exact wiring
diagrams come standard with your Alexis truck and provide
ease of electrical diagnostics. |
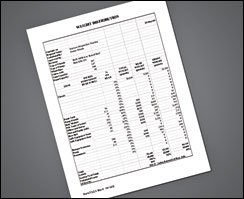
Loading Diagrams
Weight calculations insure intended
loads match correct chassis gross vehicle weight rating
during pre-planning stage. |
|
 |
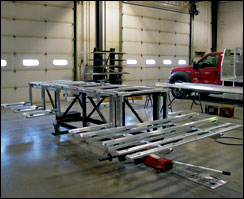
Body Subframe
A fully-welded steel subframe supports
our 3/16" thick aluminum body and allows for heavy-duty
outrigger supports under each compartment floor. A round
rubber body cushion is used to separate the steel outriggers
and aluminum angle which provide our customers with the
strongest truck body possible and the assurance that the
dissimilar metals will be separated to protect against
electrolysis. We also provide a bonded rubber surface
on the top of the subframe to protect from chaffing against
the poly water tank. |
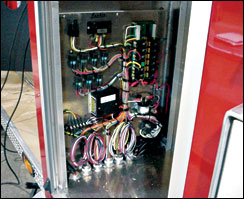
Electrical Panel
Service and maintenance is streamlined
with color, function and number code utilizing heat resistant
wiring, as well as printed circuit boards and automatic
reset circuit breakers. The connections are made through
a duetsch mechanical type connector which allows for the
best seal possible to protect against the elements. We
also now offer your department the option to utilize multiplex
electrical systems. |
|
 |
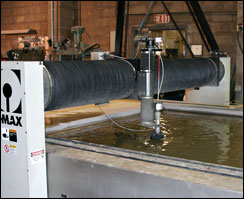 |
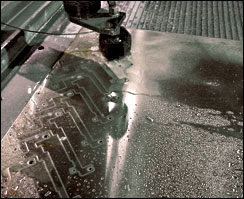 |
OMAX
50,000 PSI JetMachining Center
Alexis utilizes computer technology
and cutting-edge machines to provide optimal results.
Along with our plasma cutting machine uses high definition
plasma technology to ensure high quality results when
cutting parts, we also offer one of the fastest and most
precise abrasive waterjet cutting services in the industry
with our Omax 50,000 PSI JetMachining Center. Waterjet
machining is a computerized technology that will cut virtually
any material into any complex two-dimensional shape. Computerized
motion control provides accurate and reproducible results
efficiently throughout a wide range of materials and thicknesses
while generating a smooth edge and finish. We are able
to provide five different edge qualities, ranging from
a fast cut for material separation, to a slow speed for
a superior finished look, minimal burr, and no slag. Material
waste and overall costs are reduced by optimal part positioning
and nesting. Waterjet cutting is a clean process that
does not result in tool path heating, distortion, or residual
stress int he cut material. No heat is used so the molecular
structure of the material remains unchanged. |
|
 |
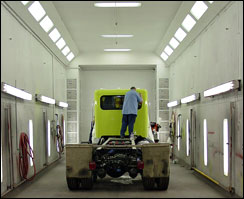 |
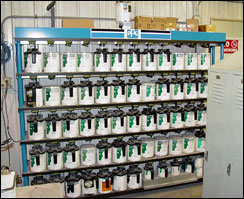 |
On-Site
Body Painting
Our apparatus bodies are painted
the Alexis premises using PPG high-gloss finish coatings.
Two coats of paint and three coats of primer for ultimate
durability and quality. The compartments can be finished
in either a natural Aluminum or Zolatone coating. Our
trucks are prepped, the paint color of your choice is
mixed, and the paint is applied to produce the finished,
painted product. |